Energy Efficiency and Firing Costs
Energy Efficiency at its best!
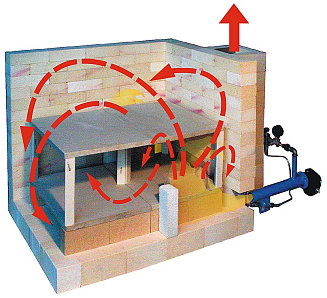
The Bailey downdraft gives a unique 360 degree heat flow pattern. This flow pattern maximizes the absorption of the heat energy and dramatically reduces firing costs. You get uniform heat top to bottom, front to back, and side to side.
Unlike venturi style downdraft kilns with burners coming through the floor, our forced air downdraft kilns offer ingenious internal adjustments to fine tune the path of the heat flow. By adjusting the placement and size of the target brick, we can optimize firing results for traditional pottery forms or sculpture. Just watch those cone packs drop evenly!
The affordable high efficiency of the Bailey combustion system is rock solid dependable, and doesn't require routine servicing. Our stainless steel burners are guaranteed for life. Compare this to kilns with computer controlled high velocity burners which are extremely expensive to purchase, expensive to maintain, require specialized service technicians regularly for tunings, and yet they don't offer any significant fuel savings compared to Bailey's highly efficient forced air system.
SOME IMPRESSIVE EXAMPLES OF BAILEY ENERGY EFFICIENCY
Some companies claim high fuel savings compared to other brands, but they aren't specific as to what these savings actually are. Maybe they are comparing their kiln to an old inefficient hard brick kiln, or an updraft kiln. Saving energy is important for our budgets and the environment. We believe in straightforward facts when we make efficiency claims, and that's what we present here for evaluation.
When you high fire in reduction, you typically find that the best quality in the reduction glazes is achieved when they have had sufficient time to develop. When a kiln is super efficient like the Bailey, it's nice to know that even if you elect to take extra time in the firing for glaze development, it will still be a super efficient firing. The type of load you intend to fire, and how you stack it, will have a bearing on the best firing schedule.
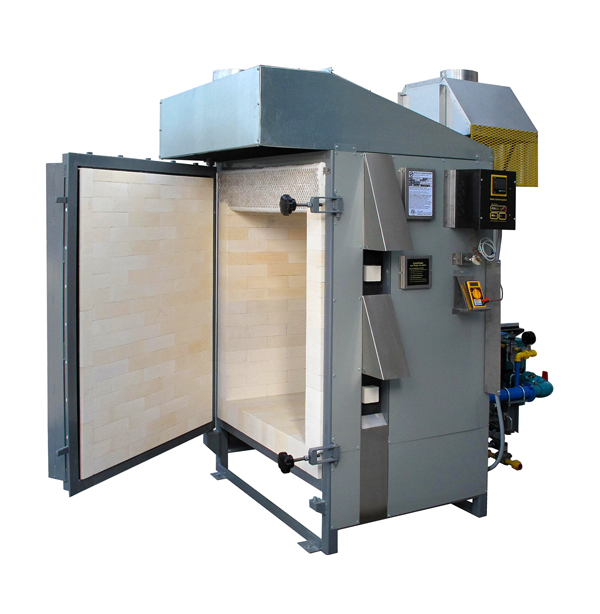
Model: | Bailey Studio Deluxe 18/12 |
---|---|
Stacking Space: | 12 cu ft |
Fuel: | Natural Gas |
Type of Firing: | Cone 10 Reduction |
Controls: | Bailey AutoFire System |
Firing time: | 7 hours |
Load Density: | Medium Stack |
Energy Consumed: | 10.8 Therms (Therm = 100,000 BTUs) |
Highest BTU/hr Setting for Firing: | 138,000 BTUs/hr |
Cost per Therm: | $1.20 (commercial rate US average 01/23) |
Cost of Firing: $12.96 |
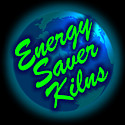
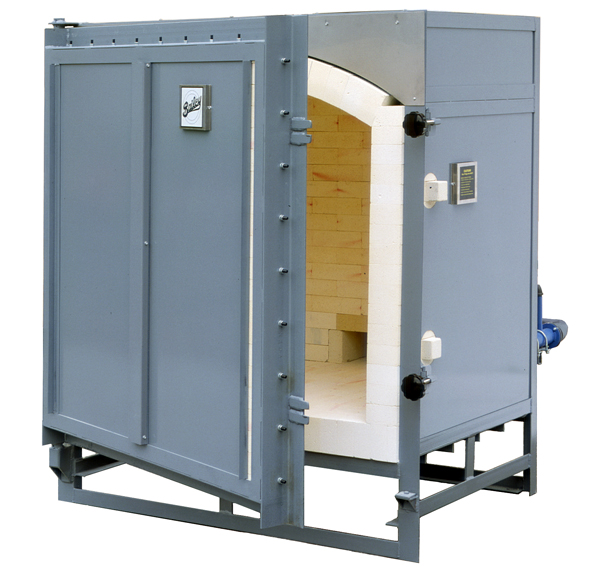
Model: | Bailey Studio Standard 48/31 |
---|---|
Stacking Space: | 31 cu ft |
Fuel: | Natural Gas |
Type of Firing: | Cone 10 Reduction |
Controls: | Bailey High Limit #1, manual controls |
Firing time: | 8.5 hours |
Load Density: | Medium Stack |
Energy Consumed: | 14.9 Therms (Therm = 100,000 BTUs) |
Highest BTU/hr Setting for Firing: | 234,000 BTUs/hr |
Cost per Therm: | $1.20 (commercial rate US average 01/23) |
Cost of Firing: $17.88 |
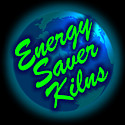
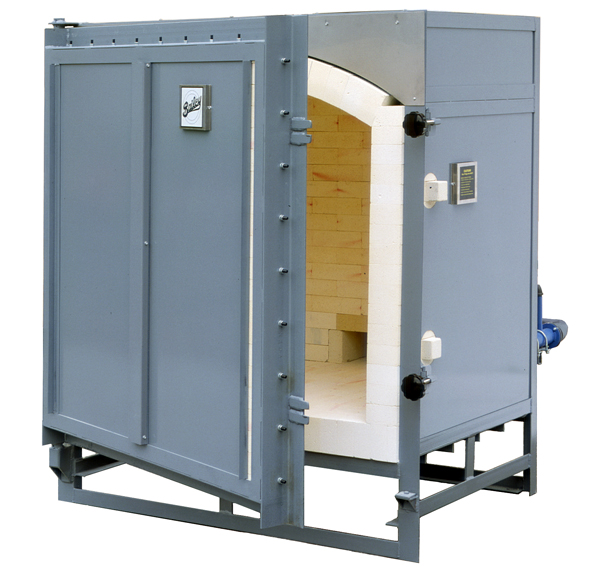
Model: | Bailey PRO 40 |
---|---|
Stacking Space: | 40 cu ft |
Fuel: | Natural Gas |
Type of Firing: | Cone 10 Reduction |
Controls: | Bailey AutoFire System |
Firing time: | 10 hours |
Load Density: | Heavy Stack |
Energy Consumed: | 19 Therms (Therm = 100,000 BTUs) |
Highest BTU/hr Setting for Firing: | 267,240 BTUs/hr |
Cost per Therm: | $1.20 (commercial rate US average 01/23) |
Cost of Firing: $22.80 |
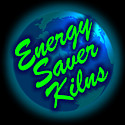
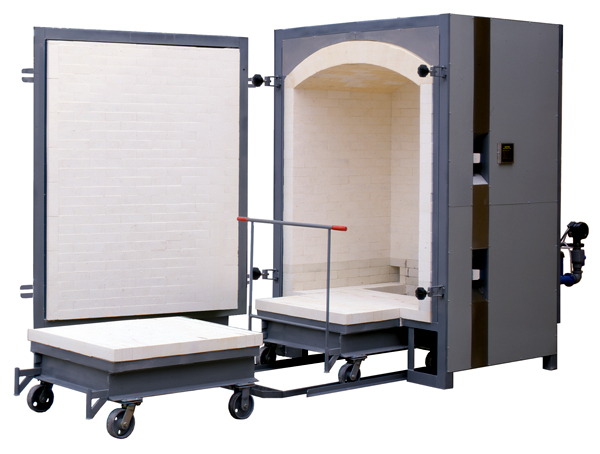
Model: | Bailey PRO 73 |
---|---|
Stacking Space: | 73 cu ft |
Fuel: | Natural Gas |
Type of Firing: | Cone 10 Reduction |
Controls: | Bailey High Limit #1 with manual controls |
Firing time: | 12 hours (by customers choice) |
Load Density: | Heavy Stack |
Energy Consumed: | 25.5 Therms (Therm = 100,000 BTUs |
Highest BTU/hr Setting for Firing: | 353,185 BTUs/hr |
Cost per Therm: | $1.20 (commercial rate US average 01/23) |
Cost of Firing: $30.60 |
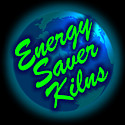
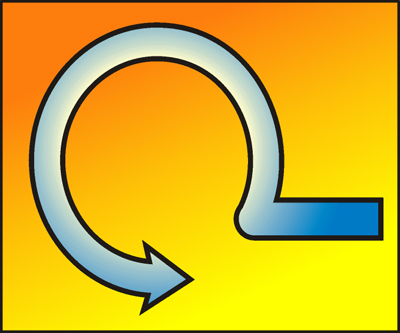
BAILEY 360 CONVECTION
The Bailey forced air downdraft provides the best of both worlds; downdraft and forced air combustion. The result is 360 degrees of convection and uniformity.
Horizontal flame entry keeps heat lower in the chamber which promotes energy efficiency, even temperature and perfect reduction atmospheres. Besides the damper adjustment, Bailey kilns have the added advantage of changing the circulation patterns to optimize performance internally by adjusting the target brick placement and shape. Burners are easily accessed for adjustment.
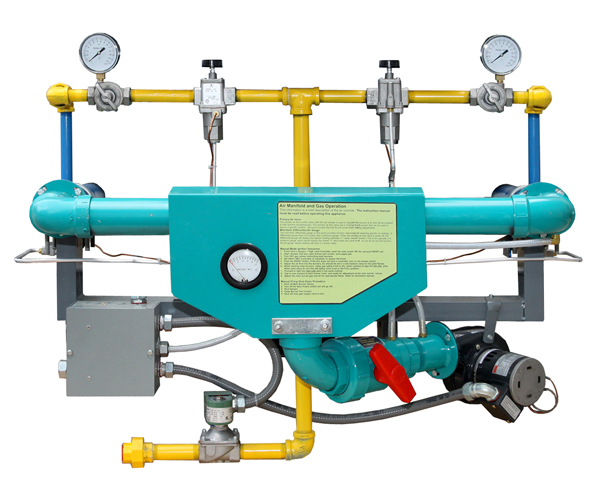
Efficient Forced Draft Burners
Forced draft burners (also referred to as forced air, or power burners) are recognized throughout the ceramic industry as the most efficient means of firing a kiln. There are several reasons why this style of burner is highly regarded.
First, the air and gas are mixed thoroughly within the main burner tube, providing complete combustion of the fuel, and reducing firing costs. Secondly, the ”forced draft” (provided by the electric blowers) maintains a constant pressure within the kiln. The constant pressure distributes the heat evenly throughout the entire kiln chamber. The flame profile (entering low, long, and horizontal) creates exceptional heat uniformity top to bottom.